ノイズ対策を行なう上で
押さえておくべきポイント
ノイズ対策の方法としては大きく「部品」と「プリント基板」に分けることができるのですが、ノイズ対策を行なうタイミング・コスト・対策期間について考えてみると、この両者には大きな違いがあります。
ひとつ目の部品によるノイズ対策は、ICなどの周辺回路で外付け部品として指定されている場合もありますが、基本的には回路全体が完成した後にノイズ対策部品として特定の周波数に対して限度を超えたノイズを押さえ込む方法となります。
対してもう一つのプリント基板上で行なうノイズ対策は、回路設計・プリント基板のパターン設計の段階で行なうノイズ対策です。この両者のノイズに対する考え方の違いは、ノイズが発生したので対策を取る(事後処理)と、ノイズが発生することをあらかじめ想定して対策を取る(事前処理)、というタイミングにあります。
上記のようにノイズ対策を事前に行なわず、ノイズが発生してから追加ノイズ対策部品によってノイズを押さえ込む方法の場合は、対策部品によるコスト上昇に加え、実装・筐体スペースの増大、さらには発熱量の増大などの問題に繋がったり、あるいは最終的にノイズが押さえ込めず機器が出荷できない、といったことに繋がる可能性が高まります。
さらにプリント基板にICなどのデバイスを実装した後、ノイズの問題が発生してからカットアンドトライで対策を行なうと、設計・製作をやり直す回数も増加するので、開発期間を短縮させるという意味においても、プリント基板を設計する段階でノイズを発生させないような十分な配慮と対策が必要となります。
2つ目に、プリント基板上で行なう対策としては、グランドを強化する対策があります。ここでプリント基板上で行なえるノイズ対策を紹介します。
例えば両面基板の場合、裏面導体が無いものと裏面全面をGNDベタとしグランドを強化した場合を比較すると、周波数全般に渡って放射ノイズレベルを低減させることができます。
また、信号ラインの処理に関しても、パターンを直角に曲げると反射が大きくなりEMIノイズが大きくなる傾向にあるのに対し、パターンを45ーで曲げたり丸く曲げるとノイズ発生の抑制につながる、ということがあります。プリント基板を設計する前段階で行なうノイズ対策にはこういった方法があります。さらに一つの考え方として、放射ノイズのエネルギーとなる高周波電流は、電子回路が搭載されているプリント基板から発生しますので、放射ノイズ対策は発生源に近いプリント基板で行なうことが効果的となります。
つまり、製品開発を始める段階で十分なノイズ対策を行なうことで、後付けのノイズ対策部品を追加する必要がなくなり、最終的には設計・開発期間の短縮や機器のコストダウンに繋がるのです。
ノイズ対策を行なう際の
シミュレーション
開発の初期段階においてプリント基板にノイズ対策を盛り込む場合は、熟練の技術者のノウハウも必要ですが、シミュレーション解析を行いその結果をパターン設計に反映させることが一般的です。 昨今では様々なシミュレーションソフトが活用されていますが、一番重要なのはシミュレーションを行なうことではなく、そのシミュレーション結果からいかにノイズを発生させないような回路やパターンに落とし込むか、ということです。 回路が複雑で信号がますます高速化する昨今の電子機器において、すべてのプリント基板上のノイズ対策を技術者のノウハウによって押さえ込むことが難しくなってきていますが、一方でシミュレーションの結果によってどのような対策を取るかも技術者のノウハウが非常に重要なポイントになります。 プリント基板のパターンでノイズ対策を行なうポイントは、①ノイズ発生源への対策(リターンパスの不連続、LSIの電源電流等)、②放射アンテナ部の対策(配線、ベタパターン等)、部品の再選定がありますが、一般的にシミュレーションツールが扱える範囲は、①と②のシミュレーション結果のみです。 ここから、どのような対策を行なえばよいのか、あるいは部品を再選定すべきなのかを判断するのは、シミュレーションを行なう技術者のノウハウによるところが大きくなります。従って、プリント基板のパターン設計を行なう場合には、シミュレーションソフトを扱うだけではなくノイズ発生に対してのトータルな技術的提案ができる会社を選ぶことが望まれます。
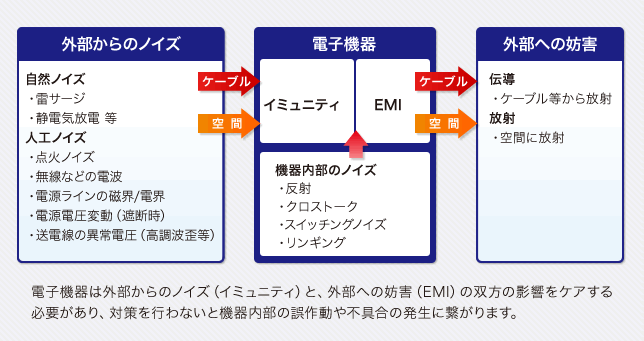